LM Vertical Roller Mill
Summary:
LM Series Vertical Roller Mill has combined the advanced Loesche technology introduced in German, MPS technique with innovative upgrading of our R&D team. For its low cost in operating, high quality of finished product, easy operation and easy maintenance,
energy saving and environmental protection, LM series vertical mill is widely used in metallurgy, electric power, cement ash, flue gas desulphurization and waste utilization, and it also has predominance in the fields of non-metallic minerals, coal and slag.
Features:
1. Low cost for investment: Integrating grinding, drying, grading and delivering. Simple structure, compact layout and open layout can significantly reduce the
costs.
2. Advanced transmission system brings high bearing capacity: New structure of gear reducer makes the machine a greater carrying capacity.
3. Hydraulic device makes maintenance more convenient: the most advanced hydraulic control system changes pressure automatically according to the materials, keeping it in the best condition, which reduces energy consumption and prolong the lifespan of roller sleeve and liner.
4. Reliable thin oil lubrication: the most advanced independent lubrication station, automatic protection system makes it safe and reliable in operation.
5. Applicable and multiple classifiers: Frequency control of separator is according to the different kind of materials and fineness. Particle size is in uniformity and easier for adjustment.
6. Electronic control system is of high automation: equipped with advanced electronic control system enable PLC, DCS and centralized control and meet multiple needs.
7. Energy saving and sustainable: less noise when working; after dust emission of the finished products, the dust density is much lower than the government standard on environmental protection.
Internal Structure:
Working Principle:
Full set of vertical mill consists of: main unit, bucket elevator, adjustable hopper, sealed constant feeder, air heating furnace, dust remover, blower and silencer. The motor drives the grinding table to rotate by reducer, and the hot air goes into the inner part of machine at the same time. The materials fall down to the center of grinding table from feed opening. Driven by the centrifugal force, materials move evenly to the edge of the grinding table, and they are grinded by the rollers when going through the rollers’ track. Bulk materials are crushed, while fine materials form material bed after
being squeezed and experience intergranular crushing. Grinded materials move on to edge of the grinding table until being taken away by strong airflow at the wind ring, in which larger materials fall to the grinding table by gravity and reground. The others enter the separator being graded. Under the influence of separator blades, materials that do not meet fineness requirements return to the grinding table to be grinded, while the standard ones go into dust collector through the pipes and are discharged as finished products from the discharge device. Irons and other impurities, which cannot be lifted by the wind for weight, move together with materials to the edge of grinding table and fall to the lower cavity, and then they are scraped into the slag discharge opening by stripper plate which is fixed at the bottom of the grinding plate and discharged out of the machine.
If you have some questions about our products, please feel free to fill out the form below, and we will contact you within 24 hours. Rest assured that we won’t reveal your information to anyone.
(Ⅰ)LM Slag Vertical Mill
1.Brief Introduction of LM Slag Vertical Mill System
LM slag vertical grinding mill is the environmental friendly vertical mill. After years of accumulations, we, in cooperation with senior experts and institutes in manufacturing vertical mill at home and abroad, developed this environmental friendly and energy-saving vertical mill. At present, the capacity of this mill has completely reached an annual output of 0.3, 0.45, 0.6, 0.9 and 1 million tons. This machine is reasonable in overall structure, advance in technology and the operation is stable. Its most technical and economic indicators have reached the international advanced level. Blast furnace slag (slag) is an industrial slag,during iron smelting, excluded from blast furnace. Due to its high physical and chemical activition and potential hydraulicity, slag is widely used as admixture in cement industry. As commonly used slag grinding equipment, slag vertical mill mainly consists of refiner disc, roller, separator, pressing device, monitoring device, gearing device,
sprinkler system and coarse powder recycling outside system, etc. These parts finish slag grinding together. Vertical slag mill has integrated drying, grinding, separating, delivering into one. Therefore, it has so many advantages such as, high grinding efficiency, big drying capacity, flexible control on product fineness, low noise, low power consumption, simple process, less frication and saving operating cost, etc, which makes it very suitable for large-scale grinding. Its main technical, economic indicators all reached the international advanced level.
2. Advantages of LM Slag Vertical Mill System
2.1 High efficiency: using rollers grind materials on the grinding disc directly consuming less energy. Compared with ball mill, it saves energy consumption by 30%~40%.As the hot air inside contacts directly with the material, drying ability is higher, and it saves energy. By regulating the air temperature, it can meet requirements with different humidity.
2.2 Less wear and tear: As the roller is not in direct contact with the disc, and material of the roller and liner is of high quality, so life lime is long and wear is less.
2.3 Stable Yield and High Quality. As materials stay in the mill for a short time, it is easy to detect and control the product’s particle size and chemical composition, which reduces repeated milling and stabilizes product quality. Moreover, roller shell and lining board don’t contact directly, so few iron are invelved into the product and these iron can be easily removed. Thus, to grind white or transparent materials, vertical mill produce product with high whiteness and purity. It is equipped with one limiting device, which
prevents the roller from contacting with the liner directly, to avoid the destructive impact and severe vibration.
3. Technical Data
Model | LM1100 | LM1300 | LM1500 | LM1700 | LM1900 | LM2200 |
Capacity(t/h) | 5~9 | 7~11 | 9~13 | 11~15 | 14~20 | 22~26 |
Raw Material Moisture | <12% | |||||
Specific Surface Area | >=420㎡/kg | |||||
Product Moisture | <=1% | |||||
Main Unit Power (kw) | 132 | 160 | 250 | 400 | 630 | 900 |
LM Cement Vertical Mill
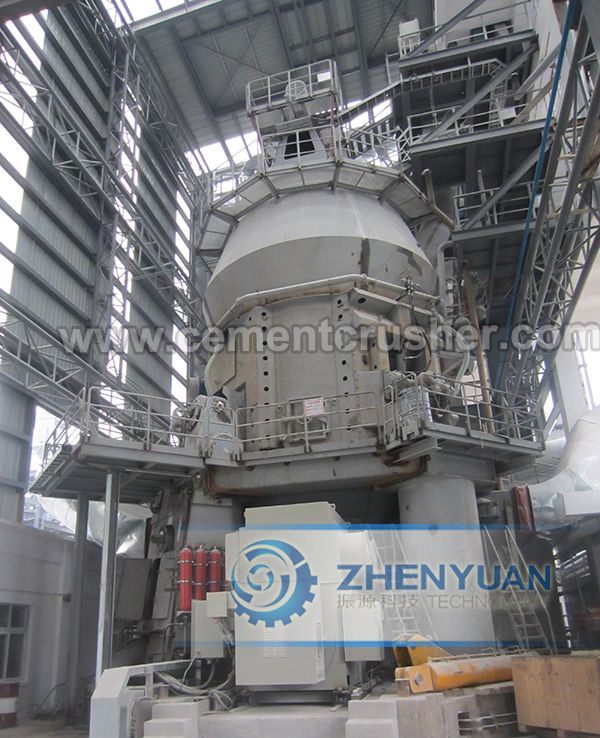
1.Brief Introduction of LM Cement Vertical Mill
Cement vertical mill, mainly used to process cement clinker, sets cement grinding, drying and classifying into one. Its biggest advantage is low power consumption: 24 ~ 27kwh / t. The cement vertical mill from Shanghai Shunky, compared with its traditional ball mill, can save electricity 30% per ton. Meanwhile, it’s an all-in-one machine, needs less auxiliary equipment, occupies a small footprint, has less dust pollution. It is the new generation of environmental friendly cement grinding equipment in line with national energy saving policy.
2. Technical Data
Model | LM1100 | LM1300 | LM1500 | LM1700 | LM1900 | LM2200 | |
Capacity(t/h) | 8~25 | 10~40 | 13~50 | 18~70 | 23~85 | 36~135 | |
Fineness | μm | 170~33 | 170~33 | 170~33 | 170~33 | 170~33 | 170~33 |
Mesh | 80~425 | 80~425 | 80~425 | 80~425 | 80~425 | 80~425 | |
Product Moisure | <=1% | <=1% | <=1% | <=1% | <=1% | <=1% | |
Feeding Size (mm) | <38 | <38 | <40 | <42 | <45 | <50 | |
Material Moisture Limited | <4% | <4% | <4% | <4% | <4% | <4% | |
Max. Moisture Limited With Drying | <15% | <15% | <15% | <15% | <15% | <15% | |
Inlet Temperature (℃) | <350 | <350 | <350 | <350 | <350 | <350 | |
Outlet Temperature (℃) | 70~95 | 70~95 | 70~95 | 70~95 | 70~95 | 70~95 | |
Main Unit Power (kw) | 132 | 160 | 250 | 400 | 630 | 900 |
LM Coal Vertical Mill
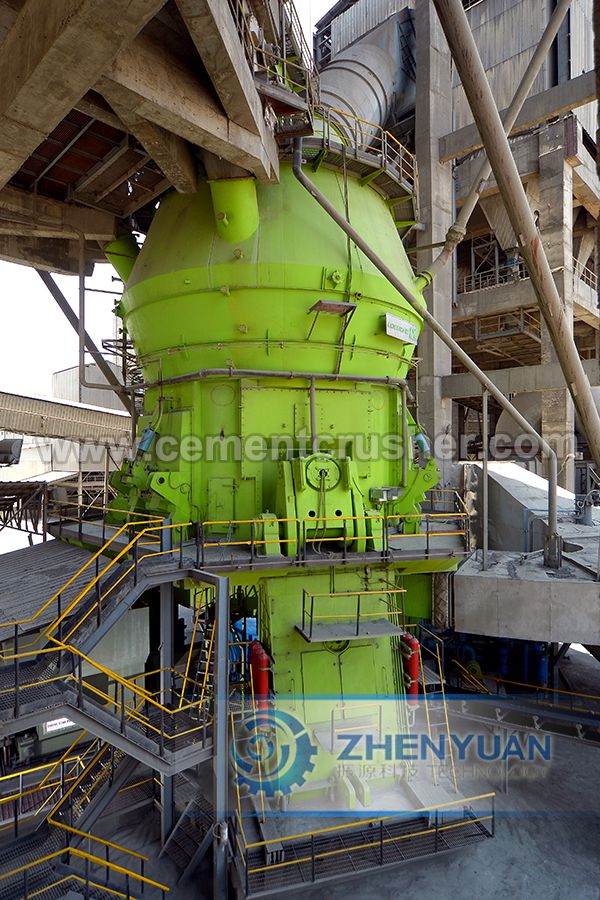
1.Brief Introduction of LM Coal Vertical Mill System
Coal from the coal yard after being sieved by the lattice screen and then fall on large inclined angle belt conveyor or elevator. The electromagnetic removes iron, belt conveyor or elevator will send the coal into the storage hopper. The milling system has been started, then open the rod valve at the bottom of the hopper, start sealed & weighted belt feeder , raw coal goes into the vertical mill for drying and grinding. The hot air or waste gas from hot blast stove, in the fan system of pumping and goes into vertical coal mill, and fully exchanges the heat with grinding coal in the vertical mill, flow the powder to air classifier and to be separated, and unqualified coarse powder falls into the grinding table to be grinded again, qualified coal powder will goes into the explosion proof air box pulse dust collector with the airflow and being collected, through the grid round are discharged into the powder bunker. The debris in the raw coal, such as partial coal gangue, metal block, etc., will be discharged out through the wind ring, spit slag . In the process of production, there are oxygen and carbon monoxide detection device, when grinding the highly volatile coal, there is a nitrogen system and carbon dioxide fire extinguishing system, safe and reliable.
2. Technical Data
Capacity(t/h) | 9~14 | 13~18 | 17~22 | 21~31 | 30~40 | 40~50 |
Raw Coal Moisture | <15% | |||||
Coal Powder Fineness 200(mesh) |
Percent Passing≥90% | |||||
Coal Powder Moisture | <=1% | |||||
Inlet Temperature (℃) | <350 | |||||
Outlet Temperature (℃) | 75~95 | |||||
Raw Coal Hardgrove Index (HGI) | >55 | |||||
Main Unit Power (kw) | 250 | 315 | 400 | 500 | 630 |
LM Metallurgy Powder Vertical Mill
Steel forging and hot rolling processing, due to the reaction of iron and steel in the air and oxygen, often form iron oxide, these material accumulate and will waste resources. If we can use the resource reasonably , can reduce the production cost, and can play a role in energy conservation and environmental protection. At present tin oxide can provide to chemical plant can be used for producing red iron oxide, yellow iron oxide, ferric
chloride, ferrous sulfate, also can produce ferrosilicon alloy, sintering raw material and producing sponge iron, high quality scrap. At the same time, it can produce iron powder by rough reduction method or refined reduction method.
SRM series vertical mill can crush or grind the broken iron oxide which less than 30mm, processing into 50-325 mesh fine powder, then the fine powder used in the metallurgy or other purposes. The finished grain production of SRM type vertical mill, with good shape, high bulk density, fully
comply with new type material’s requirements.Our company produces the SRM series vertical milling machine has been successfully applied in powder metallurgy industry, complete system stable operation, refined grain, high grinding efficiency. Bring economic value to customer, at the same time, it has also become a kind of new environmental protection equipment, saving resources.
Powder metallurgy is the process technology of making metal powder or use metal powder (or metal powder and nonmetal powder) as raw material,
through forming and sintering, to make metal material, composite materials and various types of products . Powder metallurgy method is similar to the production of ceramic, are belong to the powder sintering technology. Therefore, a series of powder metallurgy new technology can also be used for the preparation of ceramic materials. As the advantages of powder metallurgy technology, it has become the key to solve the problem of new material, which plays an important role in the development of new materials.
Powder metallurgy related enterprises are mainly used in automobile industry, equipment manufacturing, metal industry, aerospace, military industry, instrument and meter, hardware tools, electronic appliances and other fields. Products include bearings, gears, carbide cutting tools, dies, friction products, etc. In military enterprises, heavy weaponry such as armor piercing projectiles, torpedo, etc, and so on. Powder metallurgy auto parts has become the largest market in China in recent years, about 50% of the auto parts for powder metallurgy parts.
Technical Data:
Model | SRM1100 | SRM1300 | SRM1500 | SRM1700 | SRM1900 | SRM2200 | |
Capacity | 1~3 | 2~4 | 3~5 | 5~8 | 10~15 | 16~22 | |
Fineness | μm | 170~44 | 170~44 | 170~44 | 170~44 | 170~44 | 170~44 |
mesh | 80~325 | 80~325 | 80~325 | 80~325 | 80~325 | 80~325 | |
Product Moisture | <=1% | <=1% | <=1% | <=1% | <=1% | <=1% | |
Feeding Size (mm) | <30 | <30 | <30 | <30 | <40 | <40 | |
Material Moisture Limited | <4% | <4% | <4% | <4% | <4% | <4% | |
Main Unit Power (kw) | 75 | 110 | 132 | 200 | 315 | 400 |